Need a job? Learn to weld (Herald-Tribune)
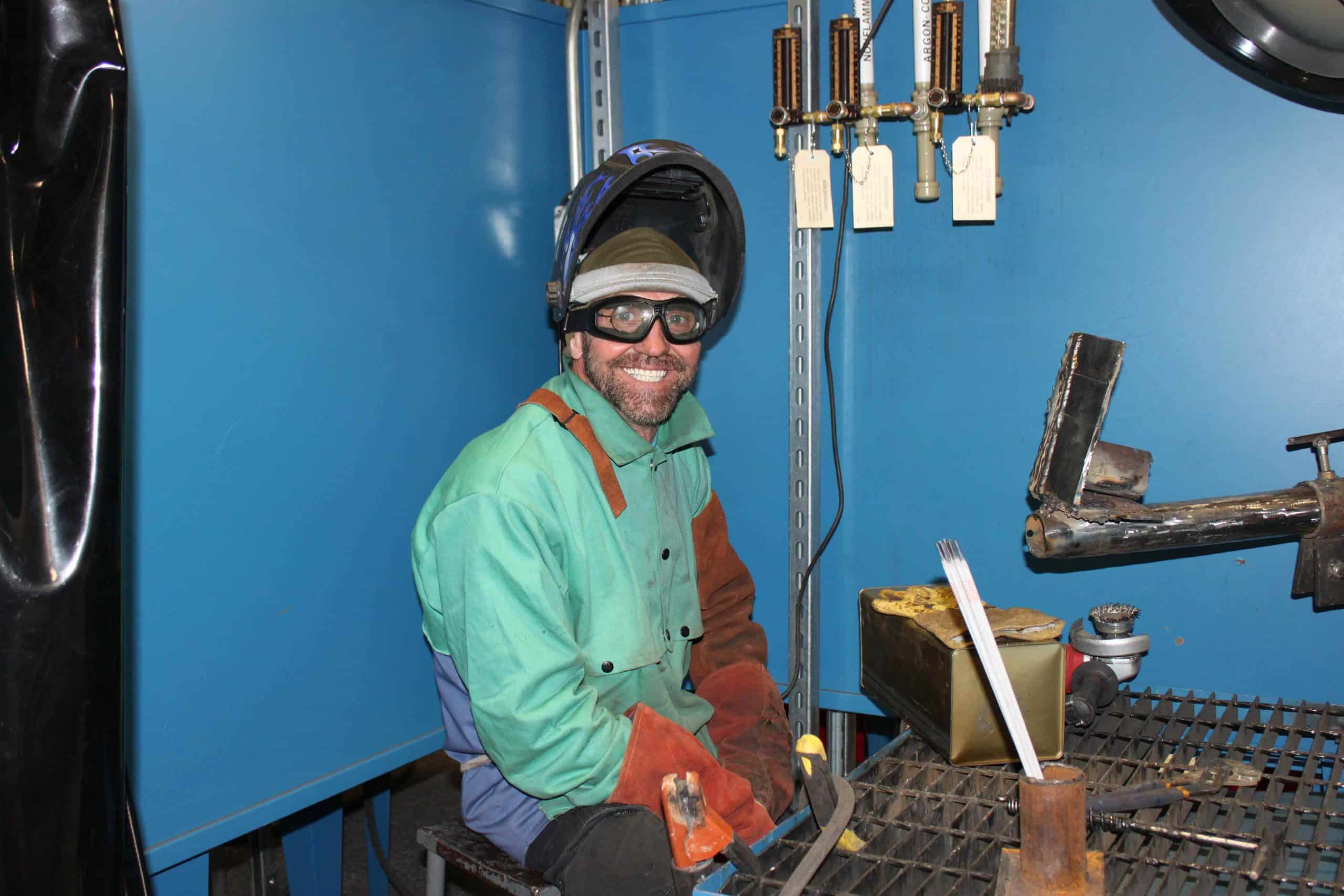
By Michael Pollick
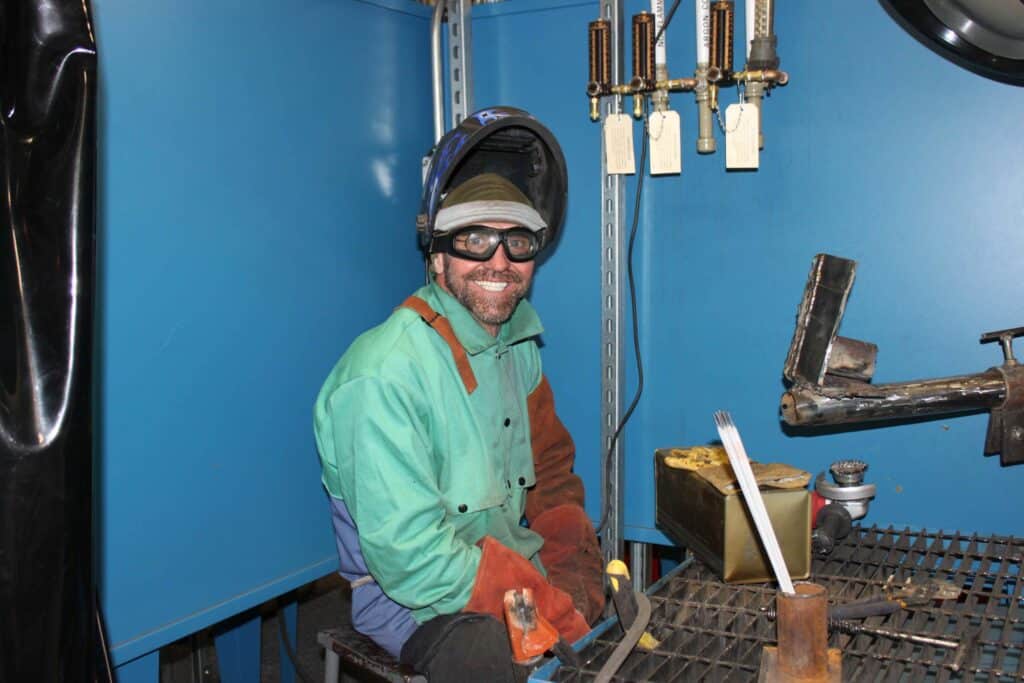
As Southwest Florida sheds the last vestiges of the Great Recession — with a resurgence in the manufacturing and the housing industries — a long slumbering problem affecting businesses is being felt once again.
You have probably heard local homebuilders complaining that the skilled laborers needed to get their industry back to prerecession par are hard to find. So many left the construction business as Manatee and Sarasota counties sank into recession, it left a staggering mark: 8,500 fewer jobs than at the peak 23,000 during the building boom.
The great welder shortage might be a new topic to many, but it is being felt just about everywhere.
A prominent National Science Foundation study found that the United States will require 250,000 new and replacement positions in just the next six years. In Southwest Florida, the current epicenter for the issue might be newcomer Air Products and Chemicals, a company building a manufacturing plant near Port Manatee.
Air Products is going to need at least 140 welders and perhaps many more as it begins building giant natural gas heat exchangers.
“They are looking to hire 10 welders a month for the next 12 months,” said Sue Downs, assistant director at Manatee Technical Institute, the main venue in Southwest Florida where someone can become a certified welder.
Extreme specialty trade
Welding by hand may sound like a 20th-century skill set, but the ability to melt two pieces of metal together — and to do it smoothly, safely and artfully — is very much in demand.
It also is mistake to think of welding as one-size-fits-all.
Some spot-weld parts together to make trailers or pick-up truck tool boxes. Others specialize in welding aluminum, others in doing repairs on oil pipelines, and still others replacing the highly pressurized steam pipes in nuclear power plants.
Sarasota County’s Andros Boat Works employs aluminum welders to make weatherproof T-tops and towers, while other marine builders often farm the work out to welding fabrication shops to do it for them.
“The kind of welding we do is different from what a traditional steel welder would do,” said Andros co-owner Andy Eggebrecht. “They have to build something from nothing.”
On one of Andros’ custom boats, the welds are a visible symbol of craftsmanship. So they have to look just right, forming delicate scalloped patterns, not just hold the tubing together, Eggebrecht said.
Air Products also is looking for welders who can do exacting work. “This is very highly skilled welding,” spokesman Art George said.
Like Andros, Air Products is willing to spend time showing recruits the exact requirements of the job, but only if they already are seen as having the right stuff. The company is working closely with MTI to screen applicants.
“Anybody can apply. Not just our students. They will go into our lab and do a test assessment on how they weld on steel and aluminum,” said Downs, the MTI assistant director. “If they pass that test OK, then we will run for them a three-week course in the evening. At that point we will zoom in on what their special requirements are.”
MTI is enrolling for classes that start Aug. 7.
For those just getting started, it is a one-year program that costs $4,000 to $4,500.
Getting older — supply and demand
The findings of the Nation Science Foundation study that showed just how big a hole American educators might have to fill with welders is not lost on local businesses or a national organization that represents welders.
“The average age of a welder is 55,” said Cindy Weihl, public relations manager at the American Welding Society, which helped complete the study. “They are retiring fairly quickly.”
While many factory jobs are being switched over to robotic welding systems, those machines still need qualified welders to run them.
“There are a lot of welding technicians who have to learn how to run these computers,” said James Heaton, MTI’s welding instructor. “But we still have construction. We still have the infrastructure of the country falling apart, and we don’t have anybody to fix it.”
“There is so much pipe under the ground, that pushes energy one place or another,” Heaton said. “They need people to fix these things.”
A decades-long focus on higher education helped create the shortage, said Weihl, of the Welding Society.
“In high school, the push was, you had to go to college for four years,” she said. “What that did, it turned people away from trade schools.”
Fairly decent pay
So what might drive this new crop of welders?
Money, for one thing — fairly decent pay relative to many of the retail and service jobs available in Southwest Florida.
A welder who reports to work in the same place each day might make $10 to $22 an hour in Southwest Florida, based on current job offers being fielded by Suncoast Workforce. Most firms offer a range somewhere between those two extremes: $12 to $18, $18 to $22, $13 to $14, $12 to $15.
Air Products did not respond with information on its pay rates.
But Mustang Vacuum, which starts welders at $17.50 per hour, “probably has one of the higher beginning pay jobs for welders in our area,” said Heaton, the MTI instructor.
Assuming full-time employment and a 40-hour work week, that would be $36,400 per year.
At Bradenton’s Tropicana Products Inc., “they might have a guy making $25 an hour. But the average guy is making $19-$20,” he said.
Willing to travel?
But the real money comes for someone who is both skilled and willing to travel.
Those welders rack up enormous overtime on jobs that absolutely, positively, have to get done on a tight schedule.
That could mean adding a new section of oil or gas pipeline across an entire state, working offshore in connection with an oil rig, or refurbishing the pipes on a shut-down power plant that has a deadline for going back into service, Heaton said.
“If you’re going to make your $100,000 a year, you’ve got to travel,” said Heaton, who figures he has been around the world one and a half times before he settled down to his teaching job at MTI.
The last job he had before retiring from the field in 2007 was worth $100,000 per year, helping to build a power plant for General Electric in California.
Heaton had a student who graduated six months ago and landed a job with a contractor who “travels pipeline.”
Still in his early 20s, the student is now making $3,500 per week, on top of a healthy per-diem allowance for living expenses. That means working 12 hours per day, sometimes six and seven days each week.
“Figure you are making $35-$40 an hour and anything over eight hours is time and a half, Saturdays are double-time, and Sundays, if it is the right job, are triple-time,” Heaton said. “You add all that up and you’re making a lot of money.”
At Tradesmen International, an Ohio company that recruits welders for traveling jobs, senior product coordinator Jeff Popek said that $3,500-per-week figure was quite possible.
“Right now welders have been in high demand,” Popek said. The trick is knowing somebody to get that first job as part of a traveling crew.
“They want people to come ready to go and know what they are doing,” Popek said. “They don’t want to take that time to show you what to do.”
“If you can get a job like shop welding, that is probably the best way to get started.”